Dispersing mechanism and application of papermaking dispersants
1. Papermaking dispersants
Dispersants are one of the main additives in the papermaking industry. At present, dispersants used in the papermaking industry are mainly aimed at two types of targets: long fibers and filler dyes. Due to the different targets, the dispersants used are also different: PEO (polyethylene oxide) and polyacrylamide are mainly used for long fiber dispersion; acrylic dispersants (sodium polyacrylate, polyacrylamide, sodium polyacrylate polyacrylamide copolymer, acrylic acid methyl acrylate copolymer) are mainly used for papermaking coating pigment dispersion.
Polyacrylamide hydrolyzate (PAM) and polyethylene oxide (PE0). PAM has a negative charge and should not be used simultaneously with other chemicals with a positive charge. PE0 is uncharged and can be used in combination with various chemical additives. It has become an indispensable additive in the production process of many special papers. However, the price of PE0 is two to four times higher than that of PAM. In addition, a large amount of foam will be generated during the production process, and corresponding measures must be taken. It is mainly used to reduce fiber flocculation and improve the uniformity of paper. For long-fiber papermaking, whether it is the previous manual papermaking or the current mechanized papermaking, dispersants must be used. This is the only way to prevent the long fibers from entanglement and drawing, and to make the paper uniform. Of course, dispersants are not only suitable for long-fiber paper, but also for short-fiber papermaking. For example, adding dispersants in the production of industrial filter paper with low beating degree can make the pore size of the paper uniform; adding dispersants in the papermaking of high-end daily paper such as napkins, facial tissues, and high-end toilet paper can improve the uniformity while improving the softness and wrinkling uniformity of the fiber.
Chemical dispersants for papermaking coating pigments mainly include two categories: inorganic dispersants and organic dispersants. Inorganic dispersants are mainly polyphosphates such as sodium hexametaphosphate, sodium tetraphosphate, sodium tripolyphosphate and sodium pyrophosphate. Organic dispersants are mainly polyacrylates as the main dispersants. In recent years, polyacrylate dispersants have developed rapidly and are being used more and more. This is because this type of dispersant can meet the high concentration and low fluidity of pigment dispersion required by high-speed paper machines, and has better time stability than dispersants without dispersants. Especially at high temperatures, polyacrylates are particularly suitable for the dispersion of calcium carbonate. When inorganic dispersants such as polyphosphates are used in calcium carbonate slurry, calcium ions and phosphates will gradually react, and the reaction rate will be significantly accelerated as the temperature rises, resulting in more polyphosphate dispersants having to be added to compensate. However, if polyacrylates are used as dispersants for calcium carbonate, the stability to time and temperature is much better. Polyacrylate organic dispersants have different properties (mainly different degrees of polymerization, that is, different molecular weights) and show different viscosities, which leads to different dispersion results for coating pigments.
2. Development of acrylic dispersants at home and abroad
Monsanto Chemical Company conducted research on the preparation method of polyacrylates in the early 1950s. Rohm and Haas Company obtained patents for the preparation of sodium polyacrylate, calcium polyacrylate and acrylic acid copolymers in the 1960s. Since sodium polyacrylate was first used as a pigment dispersant for coated paper in 1960, it has attracted the attention of developed countries. This is mainly because acrylic dispersants have the following advantages as paper coating additives:
(1) High solid coating is achieved, which saves nearly 40% energy compared with the original air knife coating. In the high concentration range (above 58%), every 1% increase in coating solid content can save nearly 2% energy.
(2) Pigment delivery pipeline and storage can be realized. When the solid content of Wen Tianji dispersant reaches 65%, it will become a dry pulp cake and cannot be canned or transported by pipeline. After adding organic dispersants, it can become a pulp liquid with a viscosity of less than 1 000mPal s, which brings benefits to pipeline transportation and canning.
(3) Improve the fineness of the pigment and the stability of the dispersion system, and improve the physical and mechanical properties of paper such as softness, strength, gloss, whiteness and water retention.
With the use of high-concentration and high-speed coating machines, acrylic dispersants are increasingly showing their superiority, new varieties and brands are constantly emerging, and application research is becoming more in-depth. In particular, sodium polyacrylate is used as a porcelain clay dispersant in the production of coated paper. In this regard, Japan, West Germany, the United States, the United Kingdom and other countries have conducted earlier and more in-depth research. Such products include SN-5040 and SN-5033 from Daxiang Meihua Company in the United States; N-40 and DL-40 from the United Kingdom; Ploystc from BASF in West Germany. At present, the main manufacturers of dispersants abroad are Rohm and Haas Company in the United States and Ocean Meihua Company in the United States.
In short, with the increase in coating with high-speed scraper coaters and the application of calcium carbonate as a coating pigment, this type of dispersant will develop further.
my country’s research, development and application work in this area began in the 1980s when the domestic introduction of acrylic monomer production lines and high-speed coating machines began. In recent years, Beijing, Shanghai, Shandong and other places have introduced coated paper production lines from Japan, Sweden and Germany, all of which are high-concentration scraper coating equipment for advanced coated paper, and at the same time, they have introduced organic dispersants produced abroad. For this reason, some acrylic organic dispersants have been developed in China. In 1984, Beijing Chemical Research Institute imitated the organic dispersants introduced from foreign countries and successfully developed DC and DA dispersants with international standards. In the same year, Beijing Institute of Chemical Technology successfully developed AM-C dispersants with sulfonic acid groups, and the products reached the level of similar foreign products. In 1985, Beijing Chemical Plant successfully developed DBH-1 dispersants, which were well received by users.
3. Dispersion mechanism of dispersants
Pigments must be used in the corresponding dispersion medium. For the coating industry, pigments must be evenly dispersed in the paint to play their coloring, decorative and protective functions. At the same time, the quality of pigment dispersion affects their coloring power, glossiness, light resistance and weather resistance.
In aqueous systems, surfactants can ionize a large number of negatively or positively charged ions in aqueous solutions. These ions can be firmly adsorbed on the surface of the paint particles, so that the ions with the same charge and the ions with opposite charges diffuse freely into the surrounding liquid medium to form a diffusion layer of charged ions, that is, a double layer. The potential difference between the two layers of ions from the pigment surface to the farthest point of the diffusion layer (i.e., the place with opposite charges of zero) is the e potential. Since ions with the same charge repel each other, a static pressure repulsion is formed, which can prevent the material from flocculating in the aqueous medium, thereby achieving the purpose of dispersion.
In the presence of electrical repulsion, the surfactant must have a high ionization property. The greater the degree of ionization, the greater the affinity of the pigment particle surface for adsorbed ions, and the more effective the dispersion effect.
Polyelectrolytes are ideal substances with this type of ionic activity. Polyelectrolytes are characterized by a large ion skeleton (a single large ion with many similar charged groups connected by chemical towns) and a small equivalent number and independent counter ion with opposite charge. The representative polyelectrolyte is sodium acrylate.
Dispersants are the most important additives in paper coatings. Their functions are:
(1) Give each pigment particle a charge, causing them to repel each other.
(2) Cover the surface of each pigment particle and play a protective role.
(3) Form a high viscosity state around the particles to prevent the particles from agglomerating, so as to ensure that the color in the coating does not flocculate and settle, and keep the viscosity of the coating as low as possible, with good fluidity and coating adaptability.
4. Other application areas
Due to the similarity of the dispersed objects, acrylic dispersants can also be used in many other fields. In addition to papermaking filler dispersion, it is also used in water-based paint pigment dispersion, water-based ink dispersion, water scale prevention, petroleum and mining industry, pharmaceutical industry, engineering plastics manufacturing, detergent production, and ceramic production.
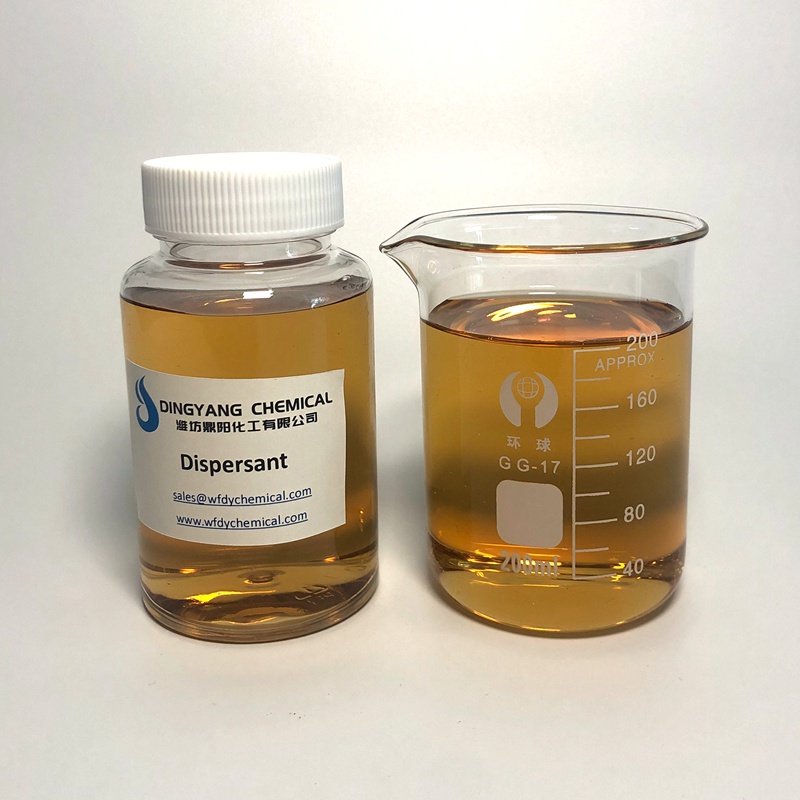